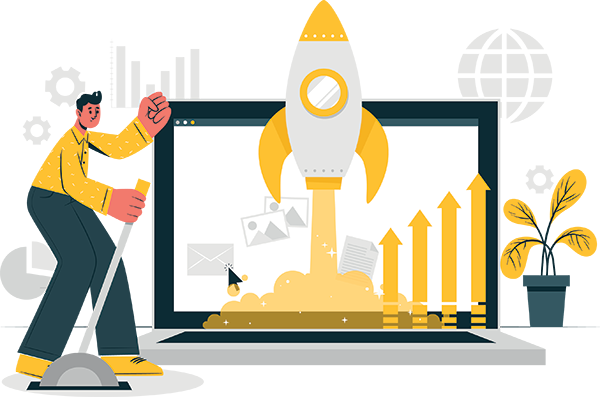
Grow Your Business
Attention Contractors! Ready to take your business to new heights? Unlock the full potential of your services and expand your reach with the power of SEO.
If you are just starting in the epoxy flooring industry or you want to take on a D.I.Y project without epically failing, we've gathered the most helpful tips from industry experts. The below tips are great for floors designed for light to medium wear and tear, such as garages and residential use.
Preparation is the key. Seriously, if you skip this step or rush it, your epoxy floor is destined to fail. As a rule of thumb, you should spend more time preparing your floor than applying epoxy. Attention to detail is the most important. Experience floor installers can sometimes spend a whole day preparing the floor on a double garage.
You wouldn't use a used canvas to paint a masterpiece, so why would you use a used floor to create a brand new floor?
Diamond grinding the floor is the best way to prepare the concrete surface and achieve the right texture for the epoxy to bond to the concrete. Grinding removes all of the dirt, grime, oil, and other contaminants from the floor, leaving you with a clean surface for rolling the epoxy.
Some epoxy floor installers, opt to use acid etching as a preparation technique, but we would not recommend it, especially if you are not experienced enough.
To achieve the right concrete texture, you have to alternate between different diamond heads, starting from coarse grit to a finer one. Grinding leaves fine concrete dust on the floor, which needs to be removed between each grind and prior to applying the epoxy.
The best way to do this is to vacuum the floor, using an industrial vacuum. Do not use a commercial vacuum, as chances are the fine dust will block the filters and ultimately break the vacuum, plus they are not powerful enough to remove all of the dust.
If you want your epoxy to properly bond with the concrete, you will need to make sure your concrete slab is free of any dust.
Your floor will have cracks and holes that will need to fill up, prior to applying the epoxy coat. This is to ensure the floor will be smooth and even. Spend time filling all of them, no matter how small they are. The best way to do it is to use an epoxy paste, a mixture of epoxy resin, and a filler powder. Use a spatula or a broad knife to fill the cracks and holes and remove any excess mixture, leaving the holes smooth.
Many people skip preparation on the floor edges as they are usually not visible. However, edges are where your floor meets the walls and where usually there is a tiny gap between the two. This is the area where your epoxy is most likely to start lifting up if hasn't bonded or applied properly.
If you are using a big grinder to prepare the floor, chances are that the edges are not prepared properly. Use a handheld grinder to run over the edges. It's time-consuming and a bit painful on your knees and back, but trust us the end result will be well worth the pain.
Once your floor is looking sparkling clean, smooth and even it's time to prepare the epoxy product for the application.
Make sure you use a quality product, as it helps with the overall finish of the floor. If you are not sure about a product, do your research. Talk to other flooring companies and see what they are using.
Most importantly, read the datasheet of the products. It contains valuable information, about how to mix it, apply it, its limitations, and pot life. Knowing the epoxy product your using, it will prevent wastage.
It might sound simple, but there is an art to mixing the epoxy coating product. You know epoxy comes in two parts - part A resin and part B hardener.
First of all, prepare your mixing station. A mixing station is a piece of plastic where you have all of your product, drill, and measuring tools. Have them all lined in a U shape, where you have one way in and one way out. This prevents tripping over or spilling any product and protecting your floor.
Before mixing the two parts, pre-stir the resin tin. Once the content of the tin is well mixed, use the measuring tools to mix both parts.
It's important to mix the product in small batches, to prevent wastage. Use your drill with a mixing attachment for easier mixing of both parts. Mix both parts for at least 2 minutes, to ensure they've fully mixed.
You can use thinners to help with the ease of application (leveling) of the epoxy resin.
Now, let’s move to the fun part of applying the epoxy coat and bringing your floor one step closer to looking awesome.
Before you start rolling, make sure you mask the floor perimeter, as this will protect the edges and walls.
Always prime your floor and don't believe claims that primer is not necessary. Priming helps seal the floor surface so the concrete doesn't blow any bubbles or gasses through your finished coat, ultimately giving your floor a longer life and better adhesion to the concrete.
Use two coats of primer, this is will help reduce the amount of product that will be required later on.
Rolling the epoxy coating on the floor comes with experience and every applicator has their own technique they have developed through the years.
The main thing to remember is to use quality roller sleeves that do not lose any hair during rolling. You don't want to have any hair marks on your finished floor, do you?
Roll around 10 sqm per person at a time. When rolling keep a wet floor edge to avoid drying before finishing the application. This will also ensure the perimeter has been fully coated.
Once you've finished with the first coat, make sure you do not miss the re-coat time frame. Re-coat time frame is the time frame in which you are allowed to apply the second coat of epoxy. You can find this info on the epoxy datasheet.
When the second coat is applied during the time frame, it activates the epoxy from the first coat in order to for the two coats to bond together. If the second coat is applied after the time frame, the epoxy will just end up sitting on top of the first coat, resulting in drying up and flaking off.
The second epoxy coat is usually applied around 13 hours after the first coat. However, between coats, you might notice holes and cracks that might need topping up with epoxy paste or that have been initially missed. Make sure these are filled before applying the next coat. You might have to also sand some uneven areas.
Once you are done with the epoxy coats, it is recommended to apply a top coat to protect your epoxy floor from scratching or UV exposure. To learn more about top coat you can read here.
Now when you have finished painting your new floor, we are sure you'll be excited to start using it.
However, there is one last thing you need to do and this is to wait until your floor is fully cured aka fully dry and ready to use.
You can find the curing times on the epoxy product datasheet, but as a rule of thumb, you should wait at least 24 hours from the last coat to start walking on it and up to 96 hours before you are able to fully use your floor.
Attention Contractors! Ready to take your business to new heights? Unlock the full potential of your services and expand your reach with the power of SEO.
We work with professionals in the home services and health industries across the USA, Australia, the UK, and Canada.
Simply leave a message and we'll get right back to you. Or call us